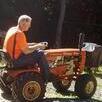
Anything special I need to know about adding a second set screw to a hub?
By
ebinmaine, in Wheel Horse Tractors
-
Similar Content
-
By wh315-8
My show tractors for October Festivals.
RJ59, 1045, 657 w/sickle bar, 10HP and D200. Just love the attention and hearing the stories of grandpa or growing up had one. Always can see the joy these Horses bring to the spectators. Than telling them the WH history story along with Speedex story always intrigues them.
Than of course there is always someone that needs to get one out of the way.
Last year it was the 1045 and the PO was so excited to learn I got her running and been mowing my grass all summer. Of course I had to let him drive her around.
This year it’s a 702 I think I getting this week.
So many were engrossed by the Sickle Bar never knowing such was available on garden tractors.
-
By Brockport Bill
NOS 1 1/8 inch hubs online price for each hub ranges $89 - $133. Used rusty hubs online sell for less $$. These NOS hubs discounted to below retail price can be bought $ 80 for each = $160 for set, plus shipping, or pick up Poughkeepsie NY area.
-
By ebinmaine
A HUGE thank you to Tony @Docwheelhorse for settin' me up here.
The generosity of some of our members never ceases to amaze me.
This here is another 1974 C160, but with the rare Tecumseh HH/OH160 OHV engine. Made one year only.
It's rough. Very much in need of a full disassembly and restoration.
When it came here it was missing one tie rod and the other was broken off one end.
Today I popped used tie rods on and Trina used her 867 to drag it from the drive to the shed.
The engine wouldn't move.
Tin was near chock full of skeletal mouseseses and their house.
Cleaned that out and the engine spins freely now.
So progress has been made.
It'll be a good long while before we get to this one but I just couldn't turn it down considering the rarity.
-
By Brian33
Hello,
I am hoping someone can help my. I recently acquired a c160 for the engine for another tractor. So I did a motor swap and wanted to see what the hydro was like. I put a plow on it C-160 (which now has a 12hp engine on it). I did a quick test run and everything was good. I drained the fluid and change the filter (Napa 1410 filter and sae 30 transmission fluid as it stated to only use this fluid on the tractor.) everything was working great after the fluid change. I plowed two driveways and the sidewalks near my house... all the sudden the tractor would not go forwards or in reverse. I tried to pick the plow up and nothing... I checked my drive belt it was turning like it should. I started to push the tractor and the rear was engaged so it would not move. Of course I was 400’ from my driveway and the plow was down which made it fun. I put the tractor in forward and started to push it and the thing took off. So I hopped on and took it to the front of the garage. I put it in revers and it cut out again so I pushed it in the garage. Today I went out to check the tow valve. I took it out and cleaned the threads up put it back in and it did not change anything. According to the dipstick I have the proper amount of fluid in it. I did have a drip that I fixed on the cylinder still nothing... does anyone out there have any tips to help me out? I’ve never had a transmission like this only manual transmissions. The model of this transmission is the sundstrand 90-1140.
Any help would be greatly appreciated.
Brian
-
By mhlmeader
Hi folks, me and the gal pal were on our way to the wheelhorse motherland ( southbend), to shop for some wedding rings. So we go down little country road see a barn sale, turned around cause I spy a wheelhorse. I ask how much , he said 400$, but someone was suppose to be picking it up. Turns out it came with a sickle bar too. My ears kinda perked up then , cause my dad wants on for his 702. They call the other fella, he passed on it, I offered 300$, we settled at 350$. Tractor runs pretty good, lil smoke when ya goose it, but runs and cuts pretty good. I'm hoping the sickle bar will fit my dad's 702, it's a 50 inch bar. Anywho, here's some pics a serial numbers if anyone has some additional info, or point me in the right direction, would be appreciated, thanks!!!
-