Countdown To Christmas!
|
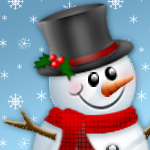
-
Similar Content
-
By wh315-8
My 50” D-series tiller input shaft has like 3/16” +\-, play pulling in or out. Anyone else have this same thing. Is it supposed to have that much play? Have it all apart and was thinking of adding a shim or 2nd thrust bearing to lessen the play to at least 1/16”.
-
By mkueb
Does anybody have a good source for replacement front wheel bearings for a mid to late 1970's D160 wheel horse tractor? There are two push in bearing units (inner and outer) per wheel. I first attempted to replace with standard bearings but quickly found out these are not standard sizes. It's been a while since I check and I don't completely remember, but I think the wheelhorse bearings where something like 1/16" of an inch larger OD than a standard catalog bearing. At the time, I remember finding bearings but they wanted somthing like $100 for each bearing. I was able to located two bearings and did purchase them for a reasonible price, but am still looking for two for completing the set. The part numbe ron the two that I was able to locate is 104396. If anybody has any ideas, I would appreciate.
Thanks
Marc
-
By Sarge
Fast question ...
Per the IPL for the 6-1141 and 6-1131 54" & 56" blades - how is everyone pinning the rear blade lock arms so they can't unlock the blade ? I've ran into problems with this thing before wanting to unlock itself and drop the blade half off the tractor. It seems when back dragging rough pavement, especially if I back into a snow bank the thing is moving those locks out of position and allowing the frame to drop off. The only reason it stays at least somewhat under the D is the lift arm , but getting it back into position is no fun due to the weight of this thing and especially out in the snow/cold weather. Last time I had to drag the thing back to a clear area so I could wrestle it back into position, lift the frame and lock it again. I did wire them shut for now, but don't trust it and I use it to back drag quite a bit on rough areas I don't want to ram the cutting edge against and risk damaging the rear axle differential or anything else. Mine has been rebuilt with a new cutting edge of 1055HC and the frame is highly beefed up - most of it is now boxed in and the thing has gained nearly 50lbs of steel. It cuts great, almost too good but that random dropping it off is starting to irritate me - need some ideas here...
The smaller 42" and other frames lock from the other direction - so to speak. The brackets are also drilled to accept large hair pin cotters to keep those locks in place - I see no way the bigger blade frame is designed for that, unless I'm missing something ?
Sarge
-
By Sarge
I've ran into a clearance issue on the D180's rear hydraulic hose at the rear of the lift cylinder for the 3pt. The link that joins the cylinder piston to the main arm on the 3pt rock shaft uses 3 holes and a welded plate between the two side sections. That plate allows the cylinder to push against the rock shaft's arm and move it rearward, but - the lower end of that plate hits the cylinder hose's 90* fitting when the lift is lowered all the way . The link only goes one way with the plate joining the two sides facing more downward than up - it's offset from being centered a bit. The 3 holes in the link allow the rear 3pt to float, if you pin the center hole it locks it solid and allows for down pressure to the 3pt lift. Simple enough design, but not sure why it wants to hit the cylinder hose's end fitting - it's wrecked the swivel on the hose and caused a bad leak. I got a new hose from Lowell, but the modern replacement hose ends are taller than the original ones from WH, so it interferes with the 90* fitting even worse - see the photo and the mark where it needs to be cut out for clearance ..couldn't get a pic of it on the tractor - that seat frame is seriously in the way of these parts. Another not so fun part to work on a D due to it's frame design...ugh.
The marked area is where it it hits that 90* fitting, badly. Aftermarket ends, as I said are even worse as they are a little taller - generally around 1/4" difference. I suspect WH specified aircraft rated low clearance fittings on many of their hydraulic hoses - it's not the first time I've ran into clearance issues , especially on the older models when replacing them with new hoses. Not sure if there is a new hose from Toro available - but it has an interference anyway with the linkage...
Has anyone else with a D ran into this issue with clearance to the link - or was this welded incorrectly from the factory somehow ?
Second thing - it seems many of the older models that used any hard steel lines used SAE 45* flare ends. Newer equipment uses the more common aircraft JIC 37* high pressure flare instead - it seats easier and can better handle the pressure. Are the steel lines on mine correct, or has someone changed them ? Ends appear to be common 5/16" SAE flares on these steel lines, it's tough to adapt modern hydraulic lines to them versus using JIC flare ends. I think even the S bend twin steel lines that go into the implement ports on the pump are the same size fittings and same SAE type versus JIS. I do remember that being odd when I had the pump out for it's repairs and all those parts looked original. A lot has been screwed with on this tractor over it's lifetime, common to see but I'm not sure just how far they went with some areas, I want to keep it correct. The old line sealed fine to the SAE hard line end below the seat - it's a 700psi system so it's fine, really. Other than the leak - the 3pt lift is super strong and had no issues other than not wanting to stay up for long due to the 90* fitting puking oil...
Sarge
-
By Sarge
Since I've finally got some time with this D and not puking oil all over itself it's time to address a few small issues . Biggest one right now is how that blade engages the ground - it always wants to sit a few inches lower on the right side and always puts more force on that side as well . When I rebuilt the frame I made certain it was squared and flat to the head part and the blade - it still measures out perfectly with the rear mount and the blade's cutting edge staying on the same plane . But , trying to do light grading work and leveling material it always wants to cut more on that right side - I suspect part of this is the weight of that handle , the solid steel cross shafts and sub frame for the whole assembly . With those parts previously cut loose I was quite surprised at just how heavy that stuff was - probably close to 35lbs of steel . With that weight hanging off one side of the frame I suspect that's the root cause of the issue - anyone got an opinion on this or ran across the same issue ?
I've considered either adding weight to the left side of the blade or maybe add a spring to the frame to help correct it - what have others done or am I by myself on this , lol ??
Sarge
-