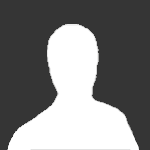
C-120 Automatic Shifting working very hard.
By
Chuck14025, in Wheel Horse Tractors
-
Similar Content
-
By giant_g2
Not sure on specific model. This 8 spd came attached to a plow I bought. It had some water in it for a couple weeks according to the prior owner. I drained it, sloshed some diesel in it, drained that, then filled with fresh oil. Spinning the input shaft by hand, I can see the axels turn. Hasn't leaked any oil. I'm not really interested in shipping, so I'd prefer local sales.
-
By Doug B
Hey guys,I have a dilemma I need some help with. I have a 1969 GT 14 that I replaced the transmission and pump on. For about 2 weeks afterward everything worked great, but while mowing at a pretty good pace I noticed a shudder and the tractor slowed a little but not bad. The more I rode it the slower it got until it barely moves. What stumps me is the hydraulics are still very strong,as in I can back the 3 point under the bumper of my truck and if you lift the arms all the way up the front wheels of the tractor will clear the ground. Have checked the tow valve and checked the internal filter,but no luck. I have also checked and replaced the forward and reverse bypass springs and the lever is moving the cam to full travel, forward and reverse. Any help would be appreciated.
-
By mattd860
I have developed a kit that allows a Wheel Horse / Toro hydrostatic tractor to be operated by a pedal on the right side of the tractor. The original forward/reverse lever can be retained or removed. The kit includes everything needed to install the pedal kit and installation is simple with the help of a downloadable installation manual. Additionally, only one (1) 1/4" hole will need to be drilled which can be done by a hand drill. No other drilling or cutting will be necessary. Any tractor with this kit can be converted back to stock without any visible evidence that kit was installed. However, you'll never want to do that
The kit operates very simply and similar to modern tractors. When the pedal is pushed forwards the tractor will move forwards. When the reverse pedal is pressed downwards, the tractor will moved in reverse. If the operator takes his foot of the pedal at any time, the pedal will automatically center itself and the hydrostatic transmission will return to neutral (stop). This enables the operator to use both hands on the steering wheel or one hand on the wheel and the other operating an attachment like a snow blower, plow, etc.
The foot pedal is custom cast in Aluminum, uses brass bushings to minimize wear, and it closely matches the OEM Wheel Horse BRAKE pedal commonly found on 8-speed manual transmission tractors. Modifications were done to the pedal to add the reverse pedal and adapt the pedal to the rest of the kit. For the most part, the pedal looks like it was designed and manufactured by Wheel Horse / Toro. Additionally, a grease fitting has been adapted to the pedal to further minimize wear and tear and if the brass bushings ever wear out they are fully replaceable without having to buy a whole new pedal.
The pedal kit fits the following series tractors with Eaton hydrostatic transmissions: C-1X5, 300, 400, 500.
My kit can be adapted to older hydrostatic tractors with the Sundstrand transmission, however, you will need to find an updated hydro cam commonly found on ebay. Message me for more information.
Here is a link where you can download the installation manual: CLICK HERE
I am selling these kits for $330 shipped to anywhere in the United States. I offer multi order discounts as well. I will also sell to other countries for additional shipping charges to be determined.
If anyone has any questions please feel free to PM me or post your question here and I will be glad to help. Or you can email me at mattdarling02@hotmail.com.
Thanks!
Below are pictures of the complete kit and the pedal installed on the tractor. Some modifications have been made since these pictures were taken. For example, the reverse pedal is now cast in aluminum instead of the steel pedal shown below.
-
By Dylan2342
New here! hello everyone! In a bit of a pickle here. My father owns a 1993 (I think that is the right year) 520H Wheel Horse. I don't commonly work on tractors but it seemed simple enough. the axle snapped on the left side, so it needed a new transmission. My dad bought a used transmission and I went to work changing everything out. The hydraulic pump that the engine's drive belt attaches to went to a different model/year of tractor, so I had to remove that part and swap it in from the old transmission. In the process I lost all of the oil in the pump (I mention this because I wonder if it has to do with my problem I'm having). When I reassembled everything I started the slow process of filling the transmission. I filled it up and started the engine. When moving the lever forward or backward, it had a tiny bit of power for a little bit and then lost power. The transmission wasn't doing anything, anymore. I though maybe that hydraulic pump needed to be primed, so we took the top hydraulic line off of the hydraulic pump right above the drive belt and used a transfer pump to pump some oil into the pump case. This still didn't work. I don't have enough experience with these hydrostatic transmissions to know if we got a bad transmission or if there is something obvious that I am missing when it comes to a transmission swap. I ask for any insight and help please. If you need pictures or any other info, then let me know what you need. Thank you!
-
By Porkskin
I have no understanding of what it is like to push one of these when the trans is disengaged and motion lever is in the forward position as the manual mentions. I hope this is not old ground and that I am not cross posting. With the trans disengaged and motion lever set forward there is still something spinning in and about the transaxle that is giving resistance. I need to know if this is normal or if I should be expecting more of a free wheeling experience. In effect, much less resistance. Thank you for comments or pointing me to a topic that already covers this.
-