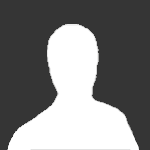
-
Similar Content
-
By WH1618speed
1965 Wheel Horse 855 with 42" blade and chains
Runs good
Sheet metal is very straight, great candidate for restoration.
Missing Belt guard
Will sell tractor by itself for $500 without blade and chains
Blade is straight and lots of cutting edge left... just a little rusty.
Text, call, or email with any questions. If you call and I don't answer please leave a voicemail with your name and number. Thanks!
I can also deliver to the big show in Arendtsville, PA... IF you prepay.
Facebook Marketplace link with more pics: https://www.facebook.com/marketplace/item/598023068755689?rid=229092436403311&ad_id&rt=1&refID=0&refType=0&referral_code=commerce_attachment
-
By Marc M.
Hi guys I'm new to the wheelhorse world and i recently picked up a for 416-H and I'm looking to buy/install a plow put on it. I have found one on craigslist but I can't tell if it will work on my tractor or not, it is a wheelhorse plow though. Can somebody please send a photo or even a video of how to hook up a plow to a 416 or equivalent tractor?
Attached is my tractor and the plow I'm looking at. Will it fix and what's it missing ?!
-
By T-Mo-(Moderator)
Drawing for both the short lift link, and the down pressure lift link for the front snow blade.
Short lift link 105052
Long lift link 7706 most likely replaced by 7706-01
I drilled 3/8" holes in the bar and used 3/8" x 2-1/2" Gr.5 bolts. Cut the threads off.
Weld the head of one bolt to the bar and try it for alignment. I ended up installing the 2nd bolt from the other direction and welding the head only. This provided 1/4" of offset and the pins are square to their attaching parts to minimise wear.
Drill holes in the bolts perpendicular to the bar for spring pins. Use a countersink to ease the edges of the holes.
With the holes drilled like they are you now know where they are and you can instal the pins blindfolded.
With manual lift the float is built in - everything floats including the lift handle.
With hydraulic lift the float is accomplished by connecting the bottom of the link to the slotted hole. Down pressure is still available when the pin hits the bottom of the slot.
Garry
-
By Goldann520
Hey guys, @wheelhorseman, @WVHillbilly520H, brought this stuff home today. Big question did wh make a gooseneck trailer like this? Really hope so, paint looks right and came out of the same lot as the rest of this. Owner swears he had blade and blower on the 414-8 Which means it'll fit my 312-8. He talked me (or bribed) me into taking tractor with me. Got the weights and chains too. $440 for all of it. Tractor runs but has fuel delivery problems.
-
By Sarge
Since I've finally got some time with this D and not puking oil all over itself it's time to address a few small issues . Biggest one right now is how that blade engages the ground - it always wants to sit a few inches lower on the right side and always puts more force on that side as well . When I rebuilt the frame I made certain it was squared and flat to the head part and the blade - it still measures out perfectly with the rear mount and the blade's cutting edge staying on the same plane . But , trying to do light grading work and leveling material it always wants to cut more on that right side - I suspect part of this is the weight of that handle , the solid steel cross shafts and sub frame for the whole assembly . With those parts previously cut loose I was quite surprised at just how heavy that stuff was - probably close to 35lbs of steel . With that weight hanging off one side of the frame I suspect that's the root cause of the issue - anyone got an opinion on this or ran across the same issue ?
I've considered either adding weight to the left side of the blade or maybe add a spring to the frame to help correct it - what have others done or am I by myself on this , lol ??
Sarge
-