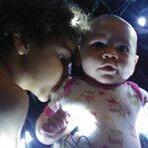
Mower deck spindles
By
ChaplainManny, in Implements and Attachments
-
Similar Content
-
By trolleybelle
Hello all, new to the forums here and relatively new to Wheel Horse. I purchased 310-8 (1989 I believe) from the daughter of its original owner last year and it came with a 42" rear discharge deck. In the past couple weeks I've been having some very loud vibration noises coming from. I removed the deck and found a lot of rub marks where the belt was hitting the deck but couldn't figure out why that was the case as the belt was nice and tight. My buddy who owns and works on wheel horses took a look at it and discovered cracking in the steel around the center spindle and theorized the spindle was oscillating up and down causing the belt to vibrate and rub on the deck. He's going to weld the deck up but told me I should source some new spindles as 2 of mine are really deteriorated.
So, short story long, does anyone know of a source for new spindles? What price can I expect to pay? I found a couple kits that have square bases but mine are round and I don't want to buy something that's not going to fit. Just looking for advice, thank you in advance!
-
By drewd
Does anyone know where I can buy new spindle housings or new spindle assemblies for this mower? 36"deck# 05-36XR01-11097; 9290. I've been working on the deck for over a year (time off for rotator cuff surgery). I started on this again when I noticed two spindles housings had been damaged. They are aluminum and as the deck is in great shape I would like to go with spindles in good shape as well.
Thanks!
-
-
By Sarge
Ok , been asked a lot of questions about how I rebuild front axles - unless they are physically broken no axle is really past the wear point of being rebuildable .
I'm starting with an early D series front axle and upgrading to a later model D series 1" spindle type with the heavier casting . Since I could never find any pics of a comparison - here we go....
If you look closely - there is an obvious difference in the castings at the spindle end - the later model axles were thicker and larger diameter to accept the heavy duty 1" spindles. Later model (post '75 , I believe).
This photo really shows the obvious difference in diameter - early models were much smaller and a thinner casting for the early 3/4" only spindles . Need to find someone with a tape measure and one of the oddball early D-200 1" spindle equipped tractors to find out if those were a thin casting or the thicker type .
The machined relief is for the roller thrust bearings that were originally used - if you ever buy a D or I believe the 520's , this is the first thing to check as many were never properly greased and destroyed that bearing . This can really wreck an expensive spindle and make it more difficult to rebuild the axle casting itself . I will be re-machining these reliefs to mimic the factory design to keep dirt out and retain the grease inside the bearing .
Early castings , at least on this 18 Auto or D-180 that I have (missing the stupid id tag completely) measures roughly 1-1/2" outside ...
Later model upgraded casting is a whole different animal - there are major differences in how they were cast and not just at the spindle ends . Later models were 1-3/4" on the outside .
Since I've never seen a new old stock replacement I'm not certain as to the original finish quality of the machining on these things - it is obvious that over time dirt has entered and a lack of proper grease results in the bores being worn badly - some are literally egg-shaped , especially tractors from the late 60's with high hours and heavy use . Snowblowers and other heavy front implements of course accelerate this wear issue - I'm out to cure that and make the unit more serviceable .
The biggest , #1 problem with these is how they are greased . I've bought and sold tractors for years and had some that had huge grease balls around the spindles , inside the wheels and all over the front end . At least they were trying but the wear is almost no different than one that was seriously neglected . With the weight on the spindle , the grease is forced upward and exits at the E-clip at the top , never lubricating the bottom where it rides on the spindle base for the steering arm .
The correct way to grease these things is to lift the tractor BY THE FRAME , NOT THE AXLE ITSELF . Also , do not lift it by the front mule quick attach - you will bend the cross rod for the latch and destroy it . Best way is to use a block on the frame itself or make a spreader to fit the jack , maybe I can take the time to get pics to show better ways to pick these things up since they aren't exactly lightweight ...lol .
No make or brand was exempt from this issue , they all did it . The problem becomes parts availability - there are only so many parts left and finding good spindles and axles is becoming a serious problem . Some brands aren't too bad (such as the green ones) since they still support most of their older models . Unfortunately for us - Toro has chosen to drop these parts and stock is quite limited . I got really lucky and a parts dealer friend had a pair of NOS 1" D series spindles , one of the last pair to exist to my knowledge . Those are getting blueprinted and angles mapped for later - I may tackle making new ones in both the 3/4" and 1" versions . I believe with a little engineering the earlier models made in the 60's could use a sort of generic spindle since there little difference in the many models - it was mostly down to the axle's angles and width .
My D will be upgraded to heim joints for the steering . Many of the tie rod and drag link ends are NLA and finding steering arms that don't have the tapered holes wallowed out is getting pretty tough . The low angle taper on those automotive style ends allows them to work loose despite having fine thread castle nuts and cotters - the force required to turn the wheels due to the above mentioned lubrication issues , combined with a gear reduction Ross type steering box makes the holes in the arms wear - I've seen 4 of these spindles on different D's all worn the same way with the tapered factory holes oval in shape and the shanks on the rod ends could be easily turned with a wrench, which should not be possible .Converting to heims is not too hard and less expensive in the long run - the only issue being the left hand threaded rod ends at the steering bell crank (or idler arm) . Since it sits so close to the underside of the frame and being tight quarters we may have to resort to using a reduced size heim joint which are easily obtained if you know the part number systems . I have a NOS pair of factory rod ends (ball joints in the parts manual) so this one won't be getting this upgrade for now .
The factory bell crank is subject to wear like everything else . It's buried up under the engine and I suspect most were neglected being so hidden . Inside is a steel bushing riding on the cast iron bore of the bell crank . The retaining bolt , bushing and iron casting all get worn - which results in sloppy steering . On a D that's a real problem since their turning radius is huge to begin with . I've modified mine slightly by moving the turning arc point of the drag link inward by 3/8" - when it's done I'll test and measure the turning radius to see how much it helped and if there is any interference or other issues . Models with working turning brakes in either the stock D-200 or kit-equipped smaller models of course helped when in dirt or grass - just never use those on pavement or hard surfaces since it can really bind things up and possibly cause rear axle damage . It's all mentioned in the manual and instructions for the kits to add turning brakes .
Not sure yet if I'll just make a separate thread on the steering parts or include them here - plenty of info to make a long thread on the cast iron axle alone . Depending upon how well it works out I may offer this as another service to the long list of other parts I build or rebuild currently . Guy with a lathe , far too many tools and a TIG welder must stay busy during the long winters....lol .
So far, it hasn't been a cheap venture - tooling bits and parts totals are well over $400 and climbing - haven't really started any machine work on the axle as of yet since I'm still waiting on one tooling bit . I will try to document what is used in the rebuild and a parts list as well as sources . All bushings and bearings used will be off the shelf parts so it's nothing that isn't easily available . Lathe work my be required to avoid using custom ordered parts and their associated extra costs .
Anyhow , more to follow....
Sarge
Going forward
-
By JackHorse
Having a hard time justifying $300 to rebuild the spindles and replace pulleys on my deck. The deck is a (i believe) 05-36MS01 on my 1982 C85. I found these kits on Pat's and was wondering if anyone had tried to adapt them to a deck like mine? Thanks
-