Countdown To Christmas!
|
Sign in to follow this
Followers
0
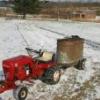
D200 Hydro Pressure issue
By
pfrederi, in Transmissions and transaxles
|
By
pfrederi, in Transmissions and transaxles