Sign in to follow this
Followers
0
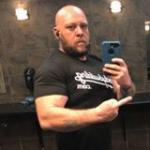
hydraulics help
By
jdog_kustoms, in Restorations, Modifications, & Customizations
By
jdog_kustoms, in Restorations, Modifications, & Customizations