Sign in to follow this
Followers
0
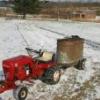
Sundstrand Piston to Piston Pressure readings
By
pfrederi, in Transmissions and transaxles
By
pfrederi, in Transmissions and transaxles