Sign in to follow this
Followers
0
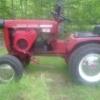
Electrical Question... Air Compressor Trouble
By
Docwheelhorse, in non tractor related discussion
By
Docwheelhorse, in non tractor related discussion