Sign in to follow this
Followers
0
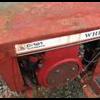
704 Hood
By
multihobbyguy, in Restorations, Modifications, & Customizations
By
multihobbyguy, in Restorations, Modifications, & Customizations