Sign in to follow this
Followers
0
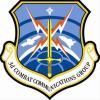
I SUCK
By
Butch, in Restorations, Modifications, & Customizations
By
Butch, in Restorations, Modifications, & Customizations