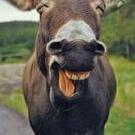
Help Needed. Automatic Return to Neutral for New Hydro Pedal
By
Bill D, in Restorations, Modifications, & Customizations
-
Similar Content
-
By HVYTWR
I have this pedal kit that I started to build for my 312 Hydro. It should fit 300, 400, and 500 series tractors. It uses a stock brake pedal from an 8 speed tractor, The link arm slides over the brake pedal and is held in place with 3 set screws. This allows the pedal angle to be adjusted separately from the linkage adjustments for operator comfort. I started to build this kit and then decided that it wasn't for me because I have very long legs and a foot control is not comfortable for me. I believe this is a pretty good design, it fits up behind the factory belt cover with no modifications. You will need to add some sort of a reversing pedal and a return to neutral device if you wish. I purchased the pedal as new old stock for $60 so it has no wear inside the bore. Then with the fabrication I have done, and the misc supplies (heim joints, rod couplers, threaded rod, lock collar, etc.) I am asking for $150 shipped. I includes everything in the photos that show the foot pedal, I will partially disassemble it for shipping. Let me know if you have any questions.
My email is wagner.rsw@gmail.com
-