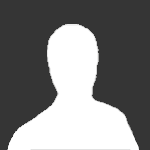
-
Similar Content
-
By rustyedge1
These belts have been hanging in my garage since last used I believe there off a 754 I used to have. Bought them new and didn't use much.
Don't know why I took them off. Some fraying on top in a few places from use, also don't know why but selling as is and photo'd. 20.00 shipped if you can use them.
PM for PayPal info or questions. 16" ID approx.
-